The slide gate plate refractory materials because of its structure, use, use conditions and other different, showing different forms of damage such as two-layer slide plate and three-layer slide plate is different, three-layer slide plate is fixed by the upper and lower slide plate, both sides of the middle slide plate are sliding surface, casting hole activity is relatively free.
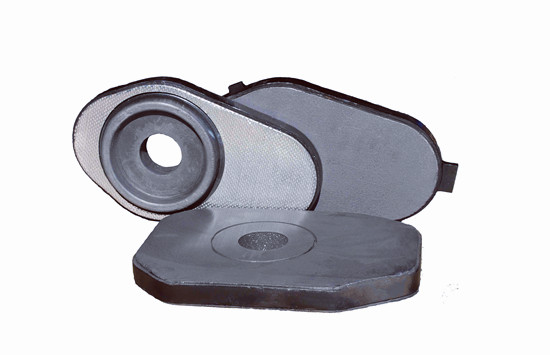
Therefore, the surface is prone to fuzziness, once the crack expansion, the casting hole in the sliding direction is more serious spalling; And the two-layer slide plate up and down the slide gate plate is fixed on the upper and lower water mouth through the child buckle, and there is only one sliding surface, so under the same conditions, the casting hole in the sliding direction of the peeling situation will be better.
The damage difference between straight reciprocating and rotary skateboards lies in the direction of cracking, but the basic damage form is not different.
The use conditions of ladle and tundish are different, so the refractory materials used for sliding plate also have different damage forms. First of all, there is almost no interaction between tundish sliding plate and slag.
And the refractory material of the sliding water outlet device in the middle package is pre-heated to about 800℃, and the temperature difference when casting steel is from the beginning of 700 ~ 800℃ to the casting steel temperature (1520 ~ 1560℃);
The refractory material of ladle sliding water outlet device is only about 100℃ before the start of casting steel, and the temperature difference of a cycle is from 100 ~ 400℃ to 1600 ~ 1670℃ each time it is used.
Tundish slide plate is not affected by thermal shock. The main reason for its damage is the wear caused by steel flow or the blockage caused by the opening and closing of fixed throttle. These factors will cause the form and degree of erosion of ladle plate and tundish plate are different.
In addition, because of the different kinds of steel and casting method (mold casting or continuous casting), the erosion and erosion degree of the slide are also different. From the analysis of the process of sliding plate damage, there are three main reasons, namely, thermal-mechanical erosion, thermal-chemical erosion and the influence of operating factors.
- Thermal mechanical erosion:
The temperature of ladle sliding plate before working is very low. When casting, the inner hole of the sliding plate suddenly contacts with high temperature molten steel (1600℃) and is subjected to strong thermal shock (temperature change is about 1400℃). Therefore, tensile stress exceeding the strength of the sliding plate will be generated outside the casting hole, leading to the formation of radiating cracks centered on the casting hole.
The appearance of cracks is conducive to the diffusion, aggregation and penetration of foreign impurities, and accelerates the chemical erosion. At the same time, the chemical erosion reaction promotes the formation and expansion of cracks, so the cycle, the skateboard casting hole gradually expanded, damaged. Moreover, the erosion of high temperature molten steel will damage the refractory near the friction part of the molten steel, causing the material spalling.
Thermal-mechanical damage mainly includes thermal-impact fracture theory and thermal-impact damage theory. The thermal impact fracture theory mainly focuses on crack nucleation, while the thermal impact damage theory mainly focuses on crack propagation.
Through a large number of practical studies, it is found that the impact resistance of commonly used skateboard refractory is compared, and the material is successively Al2O3-C, ZrO2, spinel-C and MgO-C.
- Thermochemical erosion:
Thermochemical erosion is another main reason for the damage of slide plate materials. In the process of use, refractory materials for slide plate contact high temperature steel and slag, and a series of chemical reactions occur, resulting in chemical erosion. According to the different chemical damage mechanism of different steel types to the skateboard and the different use conditions, choose the corresponding material of the skateboard, can improve the service life of the slide plate, reduce the cost of refractory materials.
Such as carbon composite refractory material skateboard: MGO-C, MgO·Al2O3-C, ZrO2 quality skateboard thermal shock stability is worse than Al2O3-ZrO2-C, suitable for special steel conditions as tundish slide plate use. Because Al2O3 and MgO·Al2O3 can react with Ca to produce low melts, MGO-C or ZrO2 sliding plates should be selected for calcium-treated steel.
Because Al2O3 and ZrO2 can react with FeO to produce low melts, so for high oxygen steel, MGO-C or MgO·Al2O3-C slide plate is selected. According to the practice of Baosteel Al2O3-ZrO2-C slide plate in the casting of the calm steel, as the tundish slide plate can be used to achieve multi-furnace continuous pouring, is not accessible to other materials of the slide plate.
No matter what kind of material, its thermochemical erosion generally includes the following forms:
(1) oxidation erosion of carbon-containing slide plate;
(2) Corrosion of refractory materials by [Ca], [Mn] and [Fe] in molten steel;
(3) the chemical change of the material contained in the refractory itself.